
My cans came from Tirantis and according to the date on the side, are 5 years past their sell by. Undeterred, I had a go anyway. The hardener label instructs the user to give the liquid a shake before use, which I did on the second attempt. Both liquids were poured (not measured) into a plastic yogurt pot and stirred with a Tamiya stirrer.

Removing the casting from the mould takes a bit of flexing and probably would be a touch easier if some release agent had been involved but I don't have any to hand and it's not essential. The tiny details still have air bubbles in them which could be fixed with filler but probably won't be since these are wagon loads and will only be seen from a distance.
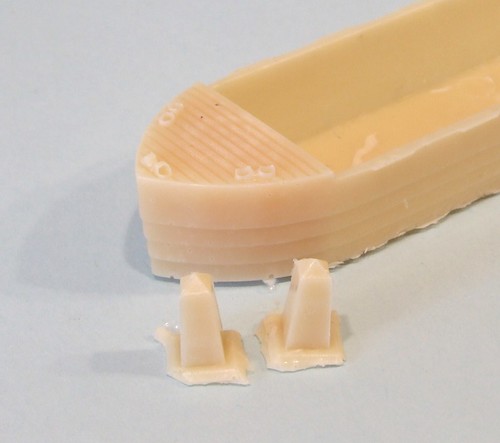
The important point is that this is all kitchen table work. No special tools are required, just 30 quid(ish) of mould material and casting resin. If you don't need the fine detail and want to make the resin go further than adding talcum powder will do the job but to be honest, it's probably not worth it. As a technique for mass-production of 3D objects, it's brilliant.
No comments:
Post a Comment